- ホーム
- 施策のご案内
- 省エネルギー
- 中部地域の省エネ応援サイト
- 企業事例 - 株式会社秋田屋フーズ
「企業全体としての利益や商品の原価を意識しながら、専門家や地域企業の協力を得て、省エネにつながる改善活動や設備更新を実践」
株式会社秋田屋フーズ
業種:製造業(チアーパック食品の生産)
株式会社秋田屋フーズ
業種:製造業(チアーパック食品の生産)
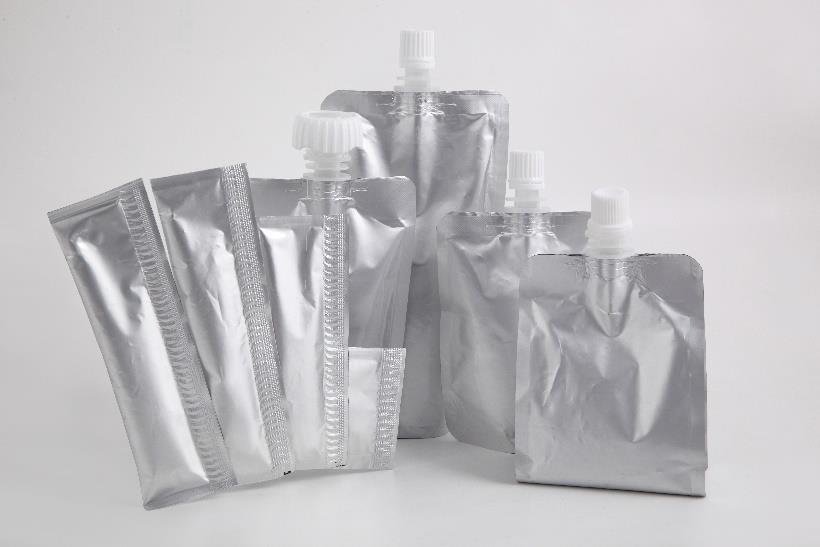
ストロー付きパウチ「チアーパック®」に充填したゼリー飲料を大手食品メーカーからOEM生産している
※チアーパック®は、(株)細川洋行の登録商標
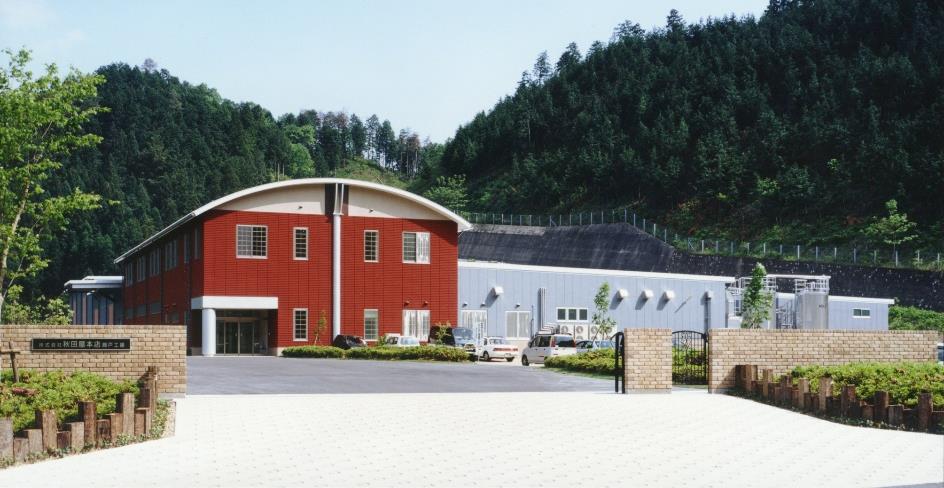
洞戸工場の外観
事業の概要
大手食品メーカー向けにチアーパック®に充填ゼリー飲料をOEM生産。秋田屋フーズは養蜂全般・蜂産品の製造・販売を展開する株式会社秋田屋本店のグループ企業。
増産体制も兼ねて殺菌冷却装置を設備更新したのを機にエネルギー使用量が増加し、第2種エネルギー管理指定工場に指定されたことで、省エネを本格的に検討するように。
省エネ診断の活用後、専門家から提案された改善策を実施するのに加え、省エネ対策を収益との関係性も考えながら自主的に検討。補助金活用によるエネルギー効率の高いLPGボイラー、コンプレッサーへの更新、RPFボイラーの導入・地域のエネルギー商社等との協働運用も実施している。
2022.4~2023.3と2023.11~2024.10の年間比較で、燃料エネルギーの28.6%減、電力資料量の2.4%減を達成。太陽光パネルによる自家発電のほか、新たな改善策の抽出と改善、設備更新時におけるエネルギー効率の高い設備への更新により、カーボンニュートラル対応を進めていく。
省エネ取組の主な概要
重油ボイラーをLPGボイラーに更新
更新時期を迎えていた重油ボイラー(1.5t(毎時))4台を、よりエネルギー効率の高いLPGボイラー(2.0t(毎時))3台に更新。
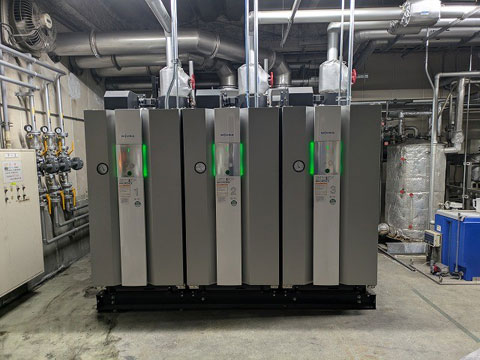
導入したLPGボイラー
熱回収コンプレッサーの導入
経年劣化していた水冷式コンプレッサー(出力37kW) 1台を、よりエネルギー効率の高い熱回収コンプレッサー(同15kW)3台に設備更新。
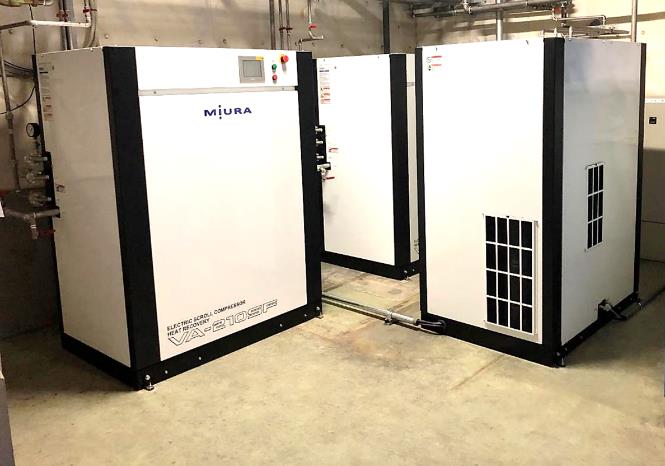
熱回収コンプレッサーの導入
RPFボイラーの導入
RPF*を燃料源とするRPFボイラーを導入。
県内のエネルギー商社・マルエイが整備工事を行い、同社の所有物として運転管理を実施。秋田屋フーズはボイラーで作った蒸気エネルギーを購入するかたちで利用。
工場の廃プラスチックの一部を地元リサイクル業者が回収してRPFをつくり、ボイラーで燃料として使用している。
※RPF(Refuse Paper and Plastic Fuel)
主に産業廃棄物のうち、マテリアルリサイクルが困難な古紙及びプラスチック類を原料とした高品位の固形燃料
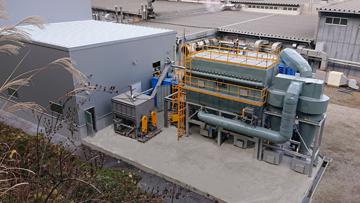
RPFボイラー(3t(毎時))
太陽光パネルを設置し、エネルギーを自家使用
オンサイトPPAモデル*で工場の屋根に太陽光パネルを設置。
発電したエネルギーを自家使用している。
*オンサイトPPAモデル
発電事業者が需要家の敷地内に太陽光発電設備を発電事業者の費用により設置し、 所有・維持管理をした上で、発電設備から発電された電気を需要家に供給する仕組み
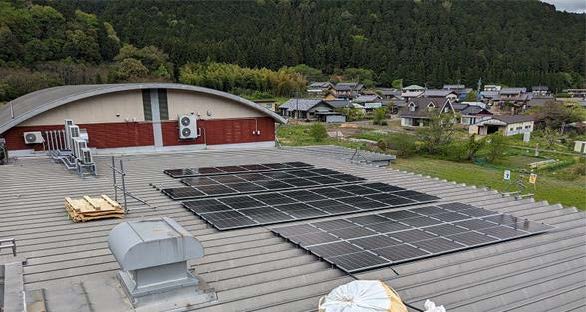
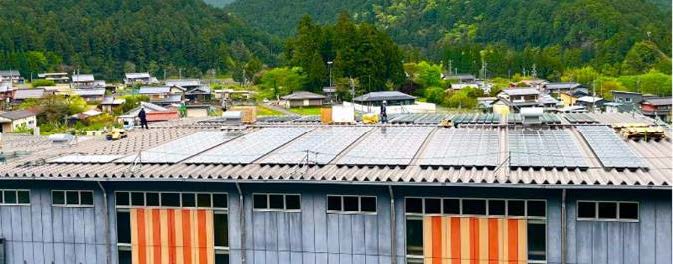
導入した太陽光パネル
省エネ取組による省エネ効果
各取組による効果
※RPFボイラーの導入 約17%のCO2排出量削減効果
洞戸工場全体における成果
(2022.4~2023.3と2023.11~2024.10の年間比較)
- ※燃料エネルギー
-
2022.4~2023.3 2023.11~2024.10 重油使用量:1295.5t(原油換算:1306.87 kL) LPG 使用量:712.25t(原油換算:933.5 kL)
※原油換算で 373.37 kL削減(28.6%減)CO2 排出量:3510.33t-CO2 CO2 排出量:2134.76t- CO2
※1375.57t-CO2(年間)削減(39.2%減) - ※電力エネルギー
-
2022.4~2023.3 2023.11~2024.10 使用量:3,795,265Kwh (原油換算:846 kL) 使 用 量:3,745,299Kwh(原油換算:826 kL)
※原油換算で 20 kL削減(2.4%減)CO2 排出量:1,643t-CO2 CO2 排出量:1,596t- CO2
※47t-CO2(年間)削減(2.9%減)
INTERVIEW
インタビュー
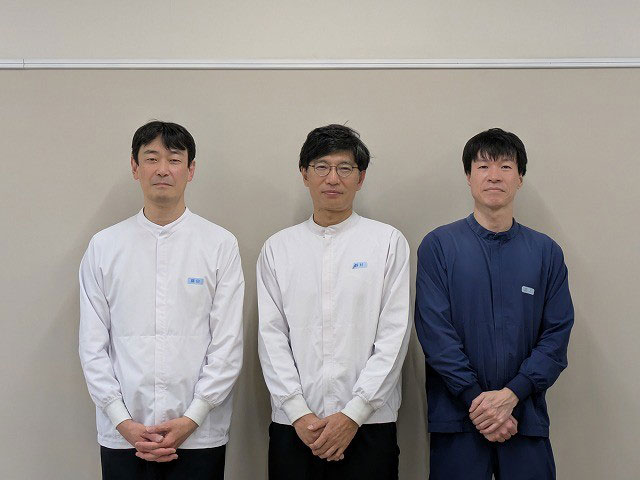
株式会社秋田屋フーズ 洞戸工場
生産統括部長 兼 工場長 藤田 尚孝 さん(左)
副工場長 野村 朝和 さん(中)
工務担当 課長 三上 良和 さん(右)
省エネの取組推進のきっかけ
設備更新を機にエネルギー使用量が増加。エネルギー管理指定工場に指定されたことで省エネを本格的に検討。
2002年4月に竣工した株式会社秋田屋フーズ洞戸工場は、岐阜県関市洞戸地区の自然豊かなところにあります。水資源が豊富で、工場敷地の周辺に設置している5ヶ所の井戸から地下水を組み上げて、大手食品メーカーにOEM供給しているチアーパック®充填を、北側・南側の2ライン体制で生産しています。
省エネについて本格的に取り組むようになったのは、2018年に北側ラインで増産体制も兼ねてパストライザー(殺菌冷却装置)を更新したときに、エネルギー使用量が増加してしまい、翌年から新たに第2種エネルギー管理指定工場に指定されるようになったことがきっかけです。早速、2019年4月にエネルギー管理委員会を発足して、何ができるかを検討するようになり、まず社内だけで実施できることとして、LED照明変更や冷暖房の設定変更などを行いました。
省エネ診断を活用。提案された改善策を一通り実施。
エネルギー管理委員会を発足した当初、省エネルギーセンターの講習会にした際に省エネ診断を知り、すぐに受診しました。提案いただいたさまざまな改善策に取り組みました。
燃料面では、ボイラーの圧力変更や、蒸気配管の保温、北側ラインのパストライザーの槽におけるドレン(蒸気の温度低下で飽和蒸気が一部凝縮し、温水に戻ったもの)の有効活用を行いました。
電力面では、北側ラインのパストライザーに設置した循環ポンプ4槽のバタフライバルブで電力調整していたものを、インバーターで調整することで電力負荷を低減しました。コンプレッサーについては、圧力設定の変更と、夏季はコンプレッサーを保有する4台のうち1台を停止しています。
また、以前からゼリーを作る調合工程の室内が暑いことが課題となっていて、空調で温度調整すると電気代があがってしまうので、どう改善するかと悩んでいました。省エネ診断でもその点を指摘いただき、熱源と作業空間をパーテーションやカーテンで遮ることで、作業環境の改善を図りました。
取組推進のポイント
省エネ診断の受診後、省エネ対策について利益との関係性も考えながら自主的に検討するように。
省エネ診断の受診後は、どれだけのエネルギー量が減るかを考えて、自主的に数値を測定するなどして改善を図るようになりました。例えば、エア漏れ検査装置を使って、設備担当で工場内の各所を測定した結果をもとに、エア漏れがあったところを数ヶ所修繕しました。空調室外機の負荷対策として室外機のまわりに水を撒いてみると、デマンドのピークが下がる効果を確認したので、今は自動で水を噴霧する装置をつけています。
隔月で開催するエネルギー管理委員会では、エネルギー使用の動向や省エネ活動についてエネルギー管理者の設備担当が報告し、情報共有しています。例えば、昨年と比べて燃料や電気の使用量、デマンドがどれだけ減ったか、今年設置した太陽光パネル(後述)の自家使用量はどのくらいあるかなどを報告し、その報告結果をもとに今後取り組むべき内容を検討しています。
また、管理委員会では、例えばチアーパック®にゼリーを充填する工程のエア漏れ改善による削減コストはいくらかを計算し、報告することもあります。省エネはコスト削減にもつながるので、企業全体として利益や各商品の原価を意識する上で重要視していて、管理委員会での報告内容や検討結果は経営層に逐一報告しています。
エネルギー効率の高いLPGボイラー、コンプレッサーに更新。補助金を活用し、コスト削減を図る。
2023年に、省エネ診断で指摘されていた重油ボイラーの改善について、11月に重油ボイラー(1.5t(毎時))4台をLPGボイラー(2.0t(毎時))3台にしました。同年12月に、経年劣化していた水冷式コンプレッサー(出力37kW)1台を、2023年12月に熱回収コンプレッサー(同15kW)3台に設備更新しました。
導入した熱回収コンプレッサーは、配管を通った冷水が熱交換されて温水になったものを、LPGボイラーに供給する水としてタンクに溜めたり、配管周りに温水を撒いたりすることで、エネルギー消費量を低減しています。
これらの設備はSHIFT 事業(環境省「工場・事業場における先導的な脱炭素化取組推進事業」)の補助金を活用して導入しました。重油ボイラーの更新をガス会社に相談していたところ、ボイラーメーカーを紹介され、そのメーカーに無料でLPG ボイラーの導入効果について調査してもらったときにSHIFT 事業の活用を提案いただきました。ちょうどSHIFT事業の申請期間のタイミングだったので、今しかないと思って申請すると交付されました。イニシャルコストの削減になったので、とても有難かったです。
RPFボイラーを導入。地域のエネルギー商社、リサイクル業者との協働で運用している。
2020年にはRPFボイラー(3t(毎時))を導入しました。きっかけは、県内のエネルギー商社・マルエイからの提案で、コスト削減が期待でき、なおかつ当社のSDGs経営に合致するものとして合意しました。
RPFボイラーは、マルエイが保有する設備を当社が場所貸しする形で設置しており、整備工事や運転管理は全てマルエイが行っていて、当社はボイラーで作った蒸気エネルギーを購入するかたちで利用しています。また、洞戸工場から出た廃プラスチックの一部は地元リサイクル業者が回収してRPFをつくり、このボイラーで燃料として使用しています。
マルエイ自身がはじめて整備されたRPFボイラーなので、安定運転に向けて試行錯誤を繰り返されていて、安定的に蒸気が出るようになったのは2022年頃だと記憶しています。将来的には、工場から出てきた脱水汚泥を燃焼処理し、産業廃棄物の処理費用のコストダウンを図りたいと思っています。
取組効果、今後の課題
省エネにかかる実績について。
エネルギー使用量(原油換算)について、2022年4月から2023年3月の1年間で重油が1,306.87kL、電力は846kLだったのが、ボイラーを重油からLPGに切り替えた2023年11月から2024年10月の1年間ではLPGが933.5kL、電力は826kLになりました。特に、重油からLPGに切り替えることで、373.37kL削減(28.6%減)とずいぶん減りました。また、生産量は増産傾向にあるので、この間に多くの商品のエネルギー原単位が燃料も電力も減っています。
RPFボイラーについては、CO2排出量が設置していた重油と比較すると約17%減となります。この取組は、エネルギーの地産地消、サーキュラーエコノミーの構築を含め、当社におけるSDGsの取組の一環として、広く情報発信しています。
また、2024年7月には夏のデマンドを抑えることを主な目的として、オンサイトPPAモデルで工場の屋根に太陽光パネルを設置し、エネルギーを自家使用しています。
新たな課題の抽出・改善、設備更新時におけるエネルギー効率の高い設備への更新を進めていく。
第2種エネルギー管理指定工場に指定されたことがエネルギーについて考え直す機会になり、自社でエネルギーに関するデータを整理し、様々な改善策を実践できるようになったように思います。
2024年8月に、岐阜県の脱炭素経営に関する助言を行う専門家派遣サービスを活用した際にも、「いろんな取組をされてきましたね」と専門家からコメントを受けました。一方で、エアの無駄を減らすことや、設備の断熱性強化など、新たな課題を指摘されたので、その点はまた社内で検討していくつもりです。
また、工場の稼働開始から20年以上経っているので、冷蔵庫やパレタイザー(出荷時等においてパレットに積み込むロボット)など、更新時期を迎えた大型設備が増えています。その際には、各メーカーと相談しながら、できる限りエネルギー効率の高い設備を導入しようと思っています。
本ページに関するお問合せ先
- 中部経済産業局 資源エネルギー環境部 エネルギー対策課
- 〒460-8510
愛知県名古屋市中区三の丸二丁目五番二号
電話番号:052-951-0417
(応対時間:9時~12時、13時~17時)
FAX番号:052-951-2568
メール:bzl-chb-shoeneteikidata■meti.go.jp
※スパムメール対策のため、@を■に変えてあります。メールを送信するときは、■を@に戻してから送信してください。