- ホーム
- 施策のご案内
- 省エネルギー
- 中部地域の省エネ応援サイト
- 企業事例 - 株式会社オーツカ
「省エネ診断を活用し、コストをかけず、知恵を使いながら、
エネルギーの見える化や省エネ活動を徹底的に追及する」
株式会社オーツカ
業種:製造業(自動車用内外装材、土木用資材の不織布の製造・販売)
エネルギーの見える化や省エネ活動を徹底的に追及する」
株式会社オーツカ
業種:製造業(自動車用内外装材、土木用資材の不織布の製造・販売)
自動車やインテリア、産業用資材等の不織布メーカー。
省エネ関連の設備更新を実施した後、経営者研修会で無料省エネ診断を知り、新たな取組を模索に向けて受診を決断。省エネ診断で、エネルギーを体系的に見える化する手法を学ぶ。
省エネ診断における工場点検を元に省エネ活用シートを作成し、診断提案に対応。テーマ別省エネ診断としてゴミ袋を使用したエア漏れ診断を社内独自で実施し、診断結果を元に設備更新を実行。
省エネ診断後の省エネルギー活動により、エネルギーの2%削減を達成。コストをかけず、知恵を使いながら、効果的なエネルギーの見える化や省エネ対策に取り組む。
取り扱っている自動車用内外装材
工場の立地状況
省エネ取組の主な概要
省エネ診断における工場点検を元にした省エネ活用シートの作成と、診断提案への対応
工場点検の後に、エネルギー合理化専門員の指導の下、省エネ活用シートを作成。
作成した結果を元に、10の診断提案を受けて実行。
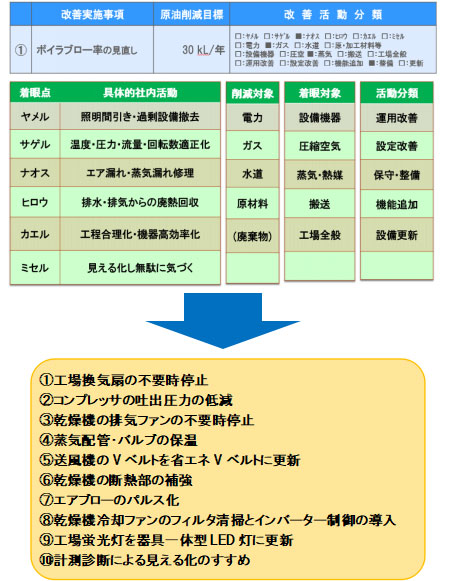
省エネ活用シートを元にした診断提案と対策効果
エア漏れ診断結果を基にしたエア漏れ対策
ゴミ袋を使った簡易エア漏れ量の計測で、具体的数値で見える化し、情報を共有。
診断結果を濡れ量、部品・部材別、濡れ量箇所別に分析し、損失金額を算出し、設備や部品の更新を実施。
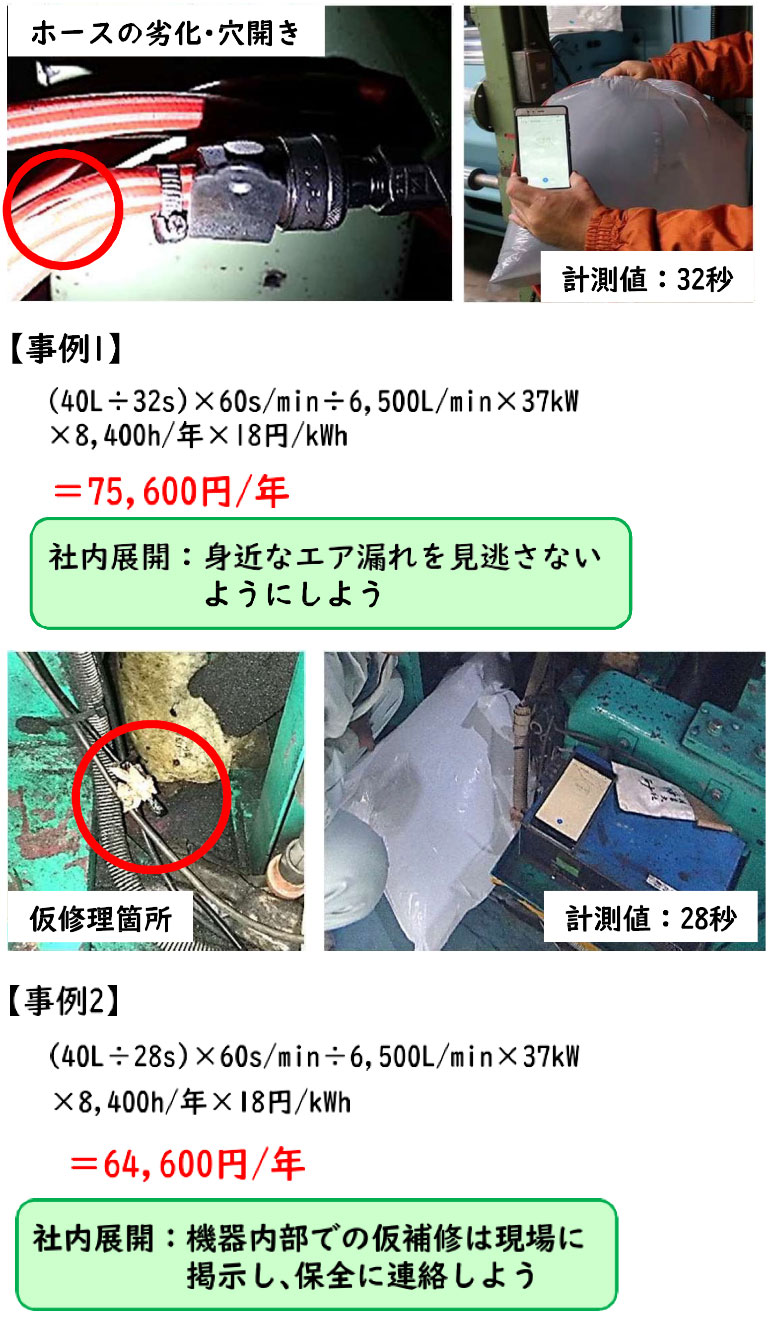
ゴミ袋での簡易エア漏れ量計測状況と年間損失金額の算出
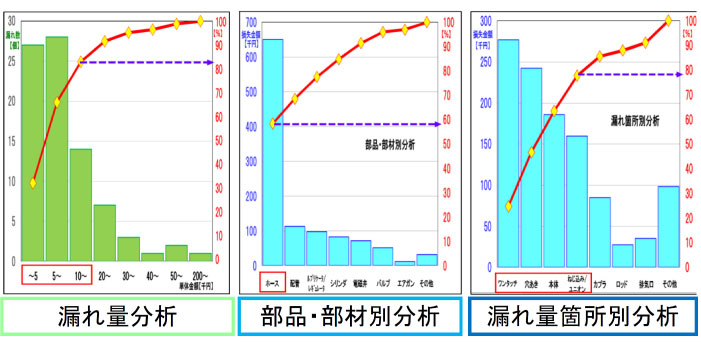
エア漏れ分析の結果
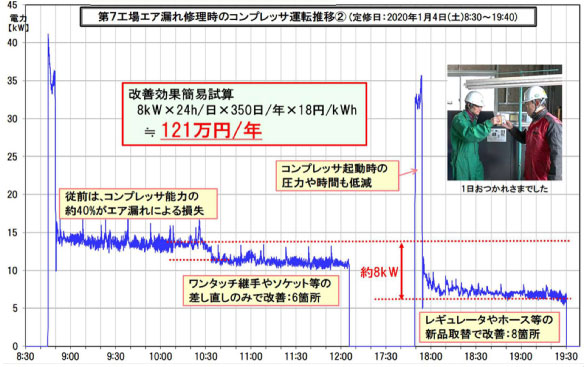
関ケ原工場第7工場におけるエア漏れ修理時の改善内容とその効果
省エネ取組による省エネ効果
省エネ診断提案への対応
-
※工場換気扇の不要時停止
省エネ効果16.3kL(年間) - 削減金額995千円(年間)
- 設備概要換気扇容量×台数×負荷率:2.2kW×10台×80%
- 運転時間:24h×350日=8400h(年間)から24h×200日4800h(年間)3600h(年間)減
- ※コンプレッサの吐出圧力の低減
- 省エネ効果9.0kL(年間)
- 削減金額547千円(年間)
- 設備概要圧縮機容量×台数×負荷率:37kW×4台×70%
- 運転時間:24h×350日=8400h
- ※乾燥機の排気ファンの不要時停止
- 省エネ効果6.3kL(年間)
- 削減金額387千円(年間)
- 設備概要排気ファン容量×台数×負荷率:11kW×8台×80%
- 運転時間:(24hから23h)×350日=(8400hから8050h)(年間)350h(年間)減
- ※蒸気配管・バルブの保温
- 省エネ効果22.2kL(年間)
- 削減金額913千円(年間)
- 設備投資額300千円回収0.3年
- 設備概要配管:32A×5m 50A×5m/フランジ:32A×20枚50A×20枚/
- 仕切り弁:32A×5台50A×5台/減圧弁:32A×10台50A×10台/
- 制御弁:32A×5台50A×5台
- 運転時間:24h×350日=8400h(年間)
- ※送風機のVベルトを省エネVベルトに更新
- 省エネ効果5.7kL(年間)
- 削減金額342千円(年間)
- 設備投資額60千円回収0.2年
- 設備概要送風機容量×台数×負荷率:5.5kW×20台×80%
- 運転時間:24h×350日=8400h(年間)
- ※乾燥機の断熱部の補強
- 省エネ効果4.8kL(年間)
- 削減金額198千円(年間)
- 設備投資額100千円回収0.5年
- 設備概要保温劣化箇所:10m2120から40℃
- 運転時間:12.5h×300日=3750h
- ※エアブローのパルス化
- 省エネ効果4.2kL(年間)
- 削減金額259千円(年間)
- 設備投資額420千円回収1.6年
- 設備概要圧縮機容量×台数:37kW×4台/吐出流量×制御:6.2~6.3m2/min×INV制御/
- パルス化機器:7000円(1台)×開閉時間比調整50%
- 運転時間:0.5h×350日=175h(年間)
- ※乾燥機冷却ファンのフィルタ清掃とインバーター制御の導入
- 省エネ効果1.8kL(年間)
- 削減金額110千円(年間)
- 設備投資額125千円回収1.1年
- 設備概要ファン容量×台数×負荷率:2.2kW×1台×40%
- 運転時間:24h×350日=8400h(年間)
- ※工場蛍光灯を器具一体型LED灯に更新
- 省エネ効果5.7kL(年間)
- 削減金額346千円(年間)
- 設備投資額1800千円回収5.2年
- 設備概要蛍光灯82WからLED灯27W/点灯時間:24h×350日×点灯率80%=6720h(年間)
- 工事込み機器費用:30千円(1台)を60台
エア漏れ対策
※関ヶ原工場第7工場における改善効果
- 削減金額1,210千円(年間)(8kW×24h/日×350日×18円/kWh[平均電力単価])
- 改善内容ワンタッチ継手やソケット等の差し直し6箇所、レギュレータやホース等の取替
事業所全体の成果
※関ケ原工場(9工場全体)
- エネルギー消費量2%削減
- (原油換算76kL、CO2では204トン、原価低減4,097千円に相当)
INTERVIEW
インタビュー
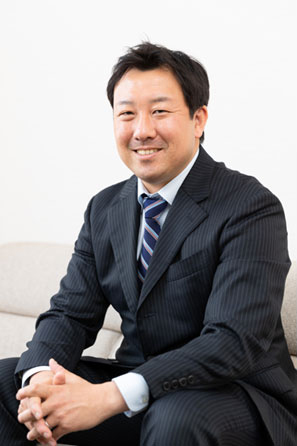
株式会社オーツカ 代表取締役 大塚 有企朗様
省エネの取組推進のきっかけ
省エネの取組はやりつくしたと思っていた中、省エネ診断を知り、実施することに。
関係企業が参加する経営者研修会で、講師で来られた省エネルギーセンターのエネルギー合理化専門員に、省エネルギーセンターによる無料の省エネ診断の話を聞いたのが取組のきっかけです。
当社の関ケ原工場は、以前より第1種エネルギー管理指定工場として、省エネに関する設備更新を実践しており、「省エネの取組は既にやりつくしたのではないか」と思っていた中、新たな取組を模索できるのではないかと思い、受診することにしました。
省エネ診断で、エネルギーを体系的に見える化する手法を学ぶ。
無料省エネ診断では、電流センサーや温湿度センサーなどでデータ取りを1、2週間行った後、エネルギー合理化専門員が中心になり、担当者と一緒に工場を回ってエネルギーを過剰に消費している箇所を指摘いただき、さらに見える化する手法を体系的に教えていただきました。
省エネ診断の成果として大きいのは、エネルギーの見える化だと思います。スポット的にデータ測定することは前々から実施していましたが、一定期間のデータを蓄積し、グラフなどで見える化するとその状況が明確になります。また、エネルギー合理化専門員と一緒に工場内を回っていくと、ポイント毎のエネルギー使用状況や、どこでエネルギーを無駄遣いしているのかもよく分かりました。
取組推進のポイント
省エネ活用シートの作成や、運用改善による効果の数値化により、省エネ活動への理解を深める。
省エネ診断では工場点検の後に、エネルギー合理化専門員の指導の下、省エネ活用シートを作成しました。省エネ活用シートでは、改善事項について、「ヤメル」「サゲル」「ナオス」「ヒロウ」「カエル」「ミセル」という着眼点で確認していくことで、それぞれがどんな省エネ活動なのかが理解でき、電気を消す・エア漏れを防ぐといった運用改善すべてが省エネ活動であると気づくことができたのが良かったと思っています。
また、運用改善による効果の算出方法については、エネルギー合理化専門員にアドバイスをいただき、省エネ効果だけでなく、コスト削減額や設備投資額なども算出しました。省エネの取組には経済合理性が一番重要で、これがないと続かないと思いますし、コスト削減は取組のモチベーションにもなります。
また、工場単位のエネルギー使用量に止まらず、設備毎に使用量を落とし込むことで、省エネ効果がより理解できるようになりました。
テーマ別省エネ診断として、ゴミ袋を使用したエア漏れ診断を社内独自で実施。
省エネ診断による診断報告書を元に、社内でテーマ別に省エネ診断を行い、対策を施しました。特に注力したのはエア漏れ対策です。
エア漏れ測定では、高価な検査機器を使わず、ゴミ袋を使って各所でどれぐらいエア漏れが発生しているかを確認し、改善によってどれくらいコスト削減できるかを試算していきました。これらの手法はエネルギー合理化専門員に教えてもらいました。
従業員に「この穴が開いたポイントを直すべき」ではなく、「これを直せば年間何万円のコストが削減できる」と伝えると、モチベーション醸成が図れますし、省エネの重要性をより理解しやすいと思います。また、投資効果がわかると、設備購入における申請や社内稟議が回りやすく、設備投資もしやすくなります。
社内での省エネ活動の取組状況や成果を積極的に情報発信。他社の省エネ診断で得た知識を社内に還元。
社内では第1種エネルギー管理指定工場として必要な管理体制を整備しており、中でも設備保全グループと製造技術グループとエネルギー管理者がコミュニケーションを密にするのに加え、社内QC活動において毎回、省エネの取組状況や成果を発表し、社内でも情報を広めるよう努めています。
また、省エネ診断でいろんな人の知識や見方が重要だと実感したので、数年前から私(野村さん)は省エネルギーセンターのエネルギー合理化専門員として、他社で省エネ診断を行っています。省エネ診断活動を通じて吸収した知識を社内へ展開し、ひいては地域貢献につながればと考えています。
取組効果、今後の課題
省エネにかかる実績について。
当社の関ケ原工場では、省エネ診断後の省エネルギー活動により、エネルギーの2%削減ができました。これは、原油に換算すると76kL、CO2では204トン、原価低減では4,097千円に相当します。
また、エア漏れ対策については、最初にエア漏れ診断を実施した関ヶ原工場第7工場では年間121万円に及ぶほどの箇所を確認し、設備更新を行いました。現在も、定期的にエア漏れ対策を行っています。
最近では、企業のSDGs経営が注目される中、お客様からは「製品の原単位に対し、どのくらいCO2を排出しているか」という質問が増えています。また、2021年に省エネ大賞 経済産業大臣賞を受賞することでお客様からの引き合いも増えており、一連の取組が当社の企業価値向上につながったように実感しています。
コストをかけず、知恵を使いながら、効果的なエネルギーの見える化や省エネ対策に取り組みたい。
「省エネをやり尽くした」と思っていましたが、省エネ診断により、社内では把握できなかった点がたくさんあることに気づき、当初の思惑通り、新たな省エネ対応策を模索することが出来ました。
エネルギーの見える化は省エネの判断基準になります。今後は設備単位に止まらず、製品単位でエネルギー使用量を落とし込み、改善に繋げることで、エネルギーの見える化を強化していきたいと思っています。
当社は中小企業なので、今後もなるべくコストをかけず、知恵を使いながら省エネ対策を進めていきたいと思っています。さらに、今後は再生エネルギーの有効活用が強く求められるようになることが予測されますので、目先の利益だけではなく、長い目で見る判断も備えることも必要だと思っています。
本ページに関するお問合せ先
- 中部経済産業局 資源エネルギー環境部 エネルギー対策課
- 〒460-8510
愛知県名古屋市中区三の丸二丁目五番二号
電話番号:052-951-0417
(応対時間:9時~12時、13時~17時)
FAX番号:052-951-2568
メール:bzl-chb-shoeneteikidata■meti.go.jp
※スパムメール対策のため、@を■に変えてあります。メールを送信するときは、■を@に戻してから送信してください。