日進工業株式会社
代変わりは変化のチャンス
自動車業界では金属部品から樹脂への代替が進み、部品点数は増加の一途を辿っている。このため、事業承継時には紙からデータ入力していた伝票枚数が月8万枚に及び、データ入力作業が大きな負担となっていた。また、システムへの反映は3日遅れになるなどリアルタイムな稼働把握とはほど遠いことから、ソフトウェア企業での経験を活かし社長自ら会社全体で何が起きているのか、必要な情報を把握するシステム開発に着手した。
生産性をつきつめる中で、機械の持っている能力を最大限発揮できるように稼働率を重視。そのためにはムダを見える化し、できるだけ機械を止めないようにすることが重要であった。
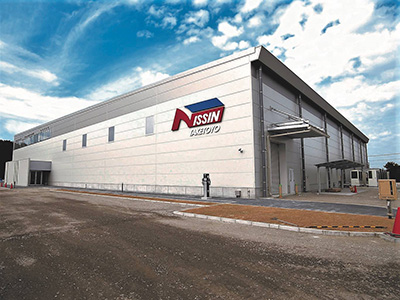
いつでもどこでも工場を見える化し、現場提案によりチョコ停の原因を解決
2015年から本格導入したMCMsystemにより工場設備の稼働状況をリアルタイムに見える化し、中国工場を含めた全社一括監視が可能となった。稼働している設備は青、停止している設備は赤で表示され、青が多ければ多いほど稼働率が高い状態にあることを示す。現場担当者が使いやすいインターフェースとなるよう画面の見やすさには十分配慮されている。
当初、数値化して正確に稼働状況を把握したところ、稼働率は予想以下の55%であることが判明したが、データの見える化とチョコ停原因のデータの累積は人の手によるカイゼン箇所の発見につながり、現在は稼働率が90%まで上がっている。
稼働率の見える化は現場の競争にもつながり、成果のあがったラインのノウハウは工程間で横展開することで、会社全体のさらなるカイゼンにつながる。また現場担当者がデータの見方を学ぶことで新たな分析や指標のアイデアもあがってくるなど、社内で自転していく仕組みが機能しシステムの高度化につながっていることに社長自身驚いている。
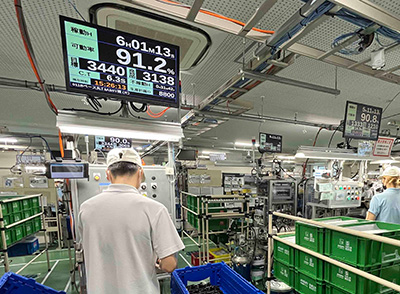
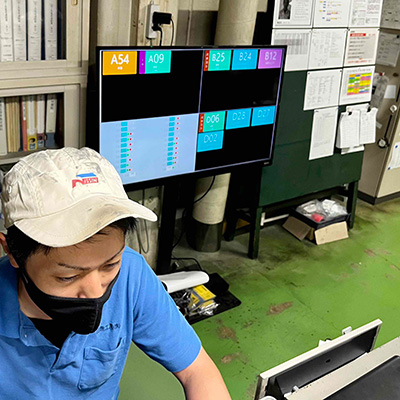
適切な人員配置でコロナを乗り越える
売上は順調に伸ばしてきたが、2020年、コロナの影響により経済活動がストップ。仕事量は4割減と当社にも大きな影響を及ぼすことになる。しかしMCMsystemは、コロナ禍でも効果を発揮し、減産と分かった時点で、かけられる人件費=必要な人員もシステムによってすぐに把握することができた。適切な人員配置により、労働生産性と利益率は低下させず、結果として減産のタイミングでも単月赤字を出さずに乗り切ることができた。
また、適切な人員配置によって生産性が上がり、残業がゼロとなるなど、結果として働き方改革にもつながっている。日頃の業務の密度をあげ、早く帰る。それでも利益が上がる体質になっているので、ボーナスとして社員に還元する。システムを導入することで社員の働き方が変わり満足度を上げることにもつながった。
DXを実践することで、予測不可能な社会環境変化にも柔軟に対応できる企業体質と変革力を身につけたと言える。
蓄積したノウハウを社外サービス展開へ
手軽に導入できる"身の丈"IoTシステムとして、現場のノウハウを外販している。まずはサンプル的にいくつかのラインを対象に見える化することで確実にムダを把握できることを実感してもらい、その上で会社全体の日々の推移をリアルタイムで把握し全体プロセスを最適化することを提案するもの。
日本の製造業は一台一台の設備の能力だけではなく、カイゼンから始まる工場全体の最適化こそに海外に負けないものづくりの強さの源泉がある。DXの取組は、その強さをさらに引き出すための最適解のひとつである。
担当後記
スマートファクトリーの実現により様々な環境変化に対応できる変革力を備えるとともに、そのノウハウをスマートサービスの提供へと発展させたDX好事例である。