ケーシーアイ・ワープニット株式会社
50年以上続く南砺市の繊維製品・製造販売メーカーの挑戦
同社はインナーウェア、アウターウェア、スポーツウェア、自動車用内装材・建築補助材料・医療関連材料等に利用される編物と織物の長所を併せ持つ「トリコット生地」の開発、製造、販売を行っている。海外製品との競争が激化するなかで、地域の産業・雇用を守るため、このままではいけない、何か変えなくてはいけないという思いから、2018年から本格的に企業変革に取り組んだ。
導入に向けた社内体制の構築
現場の作業は50年以上大きな変化は無く、「変えたくない」という風潮が強かった。さらにデジタル分野に不慣れな作業員が多数を占める状況も加わり、会社全体を巻き込んだ改革には高いハードルがあった。そのような状況の中、社長は20年間現場の業務の経験があり、保全に強い人材であった大島部長をDX推進のキーマンとして指名した。大島部長自身、現場の作業員も現状に危機感があるという点で同じ問題意識を持っていることを知っていたため、現場の作業員に対して一人ずつ丁寧に説明していくことで、DX推進に対する社内理解を得られると考えていた。
長年続けてきた業務のやり方をこの企業改革を機に見直し、次の50年を勝ち抜くためのあるべき姿を「人の力を最大化できる組織」と定め、「人の手による作業とデジタルの融合」を目指すこととなった。
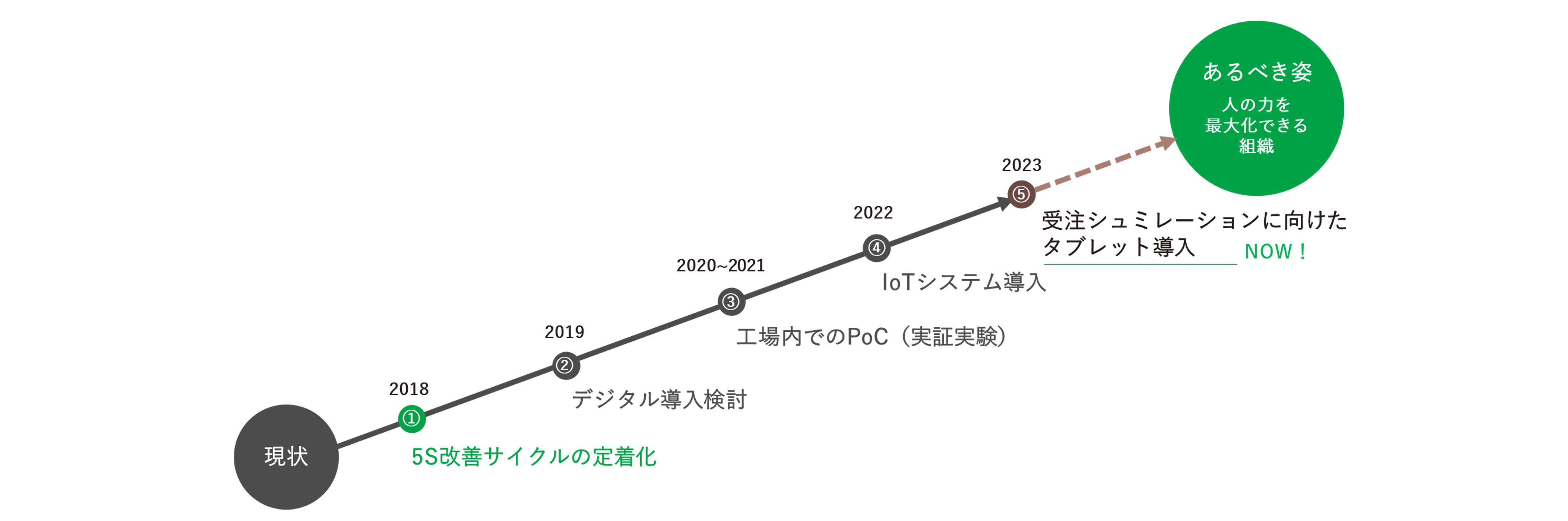
「富山県IoT推進コンソーシアム」への参加と外部人材(協力者)との出会い
当時、同社にはデジタルツール等の知識に長けている人材はいなかった。そのため、いきなりソリューションを導入するのは難しいと判断し、まずは、富山県が主体となって運営している「富山県IoT推進コンソーシアム」※に参加した。コンソーシアムが主催するワークショップでは、課題提供企業として選定され、複数のベンダー(外部人材)に対して自社の課題を提供する機会を得られた。業務フローの整理、問題発生個所の抽出、問題発生の原因の深堀をベンダーとともに実施することで、改善案を検討していった。ディスカッションでは、「まずは工場をどうしたいか」という視点から開始し、「生産を上げる」という方針を立て、自社の課題を言語化していくことで、「チョビ停を少なくする」という具体的な目標を設定することができた。
関わったベンダーの中でも特に熱心な協力者との出会いがあり、その方には、実際に現場にも足を運んでいただき「DXとは何か」という初歩の段階から、課題の抽出や対応案に落とし込む作業まで、手厚いサポートをいただいた。単にツールを導入するのではなく、直接現場の管理者にヒアリングし検討を進めてもらう等、DXの総合プロデューサーのような立ち位置で活躍していただいた。
(※富山県IoT推進コンソーシアム:産学官金が互いに交流しながら、IoTなどの導入活用に関わる情報提供や意見交換、交流する機会を設け、県内企業等の生産性向上や新たなサービス・付加価値の創出を目指し、平成29年9月に設立した組織。)
デジタル導入検討にかかる工場内での実証実験
「チョビ停が多い」という課題の解決が、生産性・収益の改善に繋がることを実証するために、工場の「見える化」が必要という考えにいたった。そこで、最初に「共有型とやまものづくりIoTプラットフォーム」※ を活用し、いくつかのセンサーの利用を試みたが、当時選択できたセンサーの種類では編み機の稼働状況は正確に取得することができなかった。例えば、加速度センサーで振動を計測することは一般的だが、他の機器や重機の移動などによる振動の影響を受け、編み機の稼働状況は正確にとることができなかった。また、スイッチ(押しボタンセンサー)による入力も試みたが、自動ではないことに加え、扱える情報量も少なく、現実的ではないという結論にいたった。作業員には年配の方や外国人の技能実習生もいたため、現場を理解している大島部長としては、作業的な負担がないかたちでのDXの実現を目指していた。
(※共有型とやまものづくりIoTプラットフォーム:複数の企業で簡易的なIoTシステムを共同利用する仕組み)
その後、長期間にわたり同業他社の見学や勉強会を実施した末にCTセンサー(電流センター)の活用という答えを見出し、3か月間実証実験を行った。その結果、稼働状況のデータを正確に取得することが可能となり、求めている「見える化」のイメージと近いものが得られると分かったため、富山県の補助金を活用し導入することとなった。
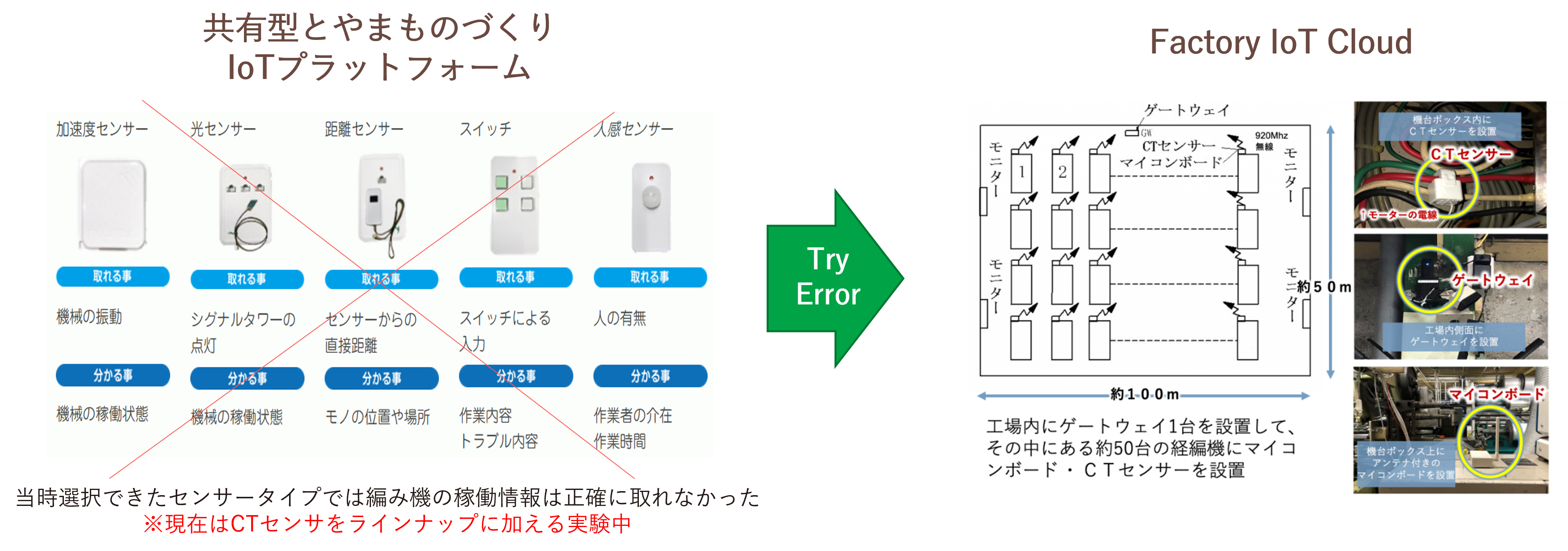
IoTシステム導入後の運用
編立部の工場内に4か所モニターを付けて、稼働している時は緑、停止状態の時は赤になるようにし、停止した理由を入力することで表示されるようにした。導入後もより細かい情報を入力できるように現場作業員でシステムを改善しており、改善の一つに停止の表示方法の修正がある。具体的には、停止の際の表示が赤になるだけではなかなか気づかないため、時間が経つと点滅に変わるようにすることで、早く対応することが可能となった。結果として、システム導入前と比較して労働生産性が2%上がっている。
また、現場のモニター表示においては、全体の稼働状況とブロックごとの稼働状況の画面を一定周期で切り替わるように設定した。全体の稼働状況を遠くからでも一目で把握できるよう、実際の工場内の機器の配置で表示し、稼働状況も色で分かるようにした。加えて、現場の作業者だけではなく管理者もデータを確認でき、停止時間や理由等も含めて、蓄積されたデータを集計することもできるようになった。
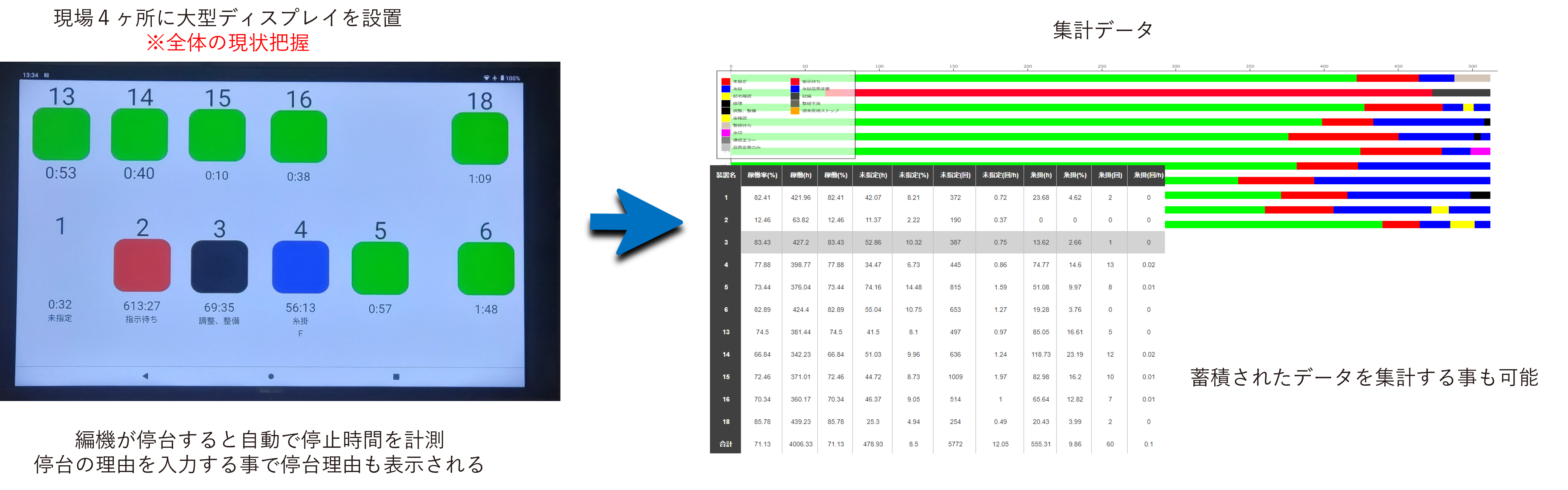
「DX Selection 2023」の選定とDX推進による社員の行動変容
同社のDX推進の取組については、優良事例として「DX Selection 2023」にも選定されている。この取組は一時的なものに留まらず、社内の意識改革を経てIoTによる機械の稼働状況の見える化に成功したことにより、自身の業務以外に関心のなかった作業員が機械の稼働ディスプレイを見て行動する「行動変容」に発展した。
社会課題と生産性向上
「物流の2024年問題」を始めとした社会課題が外的要因となる影響は大きい。特に、人材不足の問題は深刻であり、無人化・省力化に目を向けていく必要がある。このような状況の中でも、いかに生産を上げていくかということが課題である。現在は、準備工程のデジタル化を進めており、実現すれば受注シミュレーション(デジタルツイン)が可能となる等、同社の改革は現在も継続している。